Commercial Concrete Services
START BUILDING YOUR NEXT BIG INVESTMENT
COUNT ON US FOR COMMERCIAL CONCRETE CONSTRUCTION SERVICES IN THE FORT WORTH, ARLINGTON, MANSFIELD, GRANBURY, AND SPRINGTON WEATHERFORD AREAS
Maintaining and upgrading your commercial property is vital to its continued success. Boone Construction Services, LLC offers commercial concrete services throughout Mansfield, Aledo, Weatherford, Irving, Arlington, and Dallas-Fort Worth, TX. Our team provides both installation and replacement services for paving and driveways. We also handle all types of new concrete foundation and replacement work.
Do you live outside of Weatherford, Texas? We will perform your construction needs in Dallas, Fort Worth, Arlington, Mansfield, Aledo, and beyond. All estimates are free, and no project is too large!
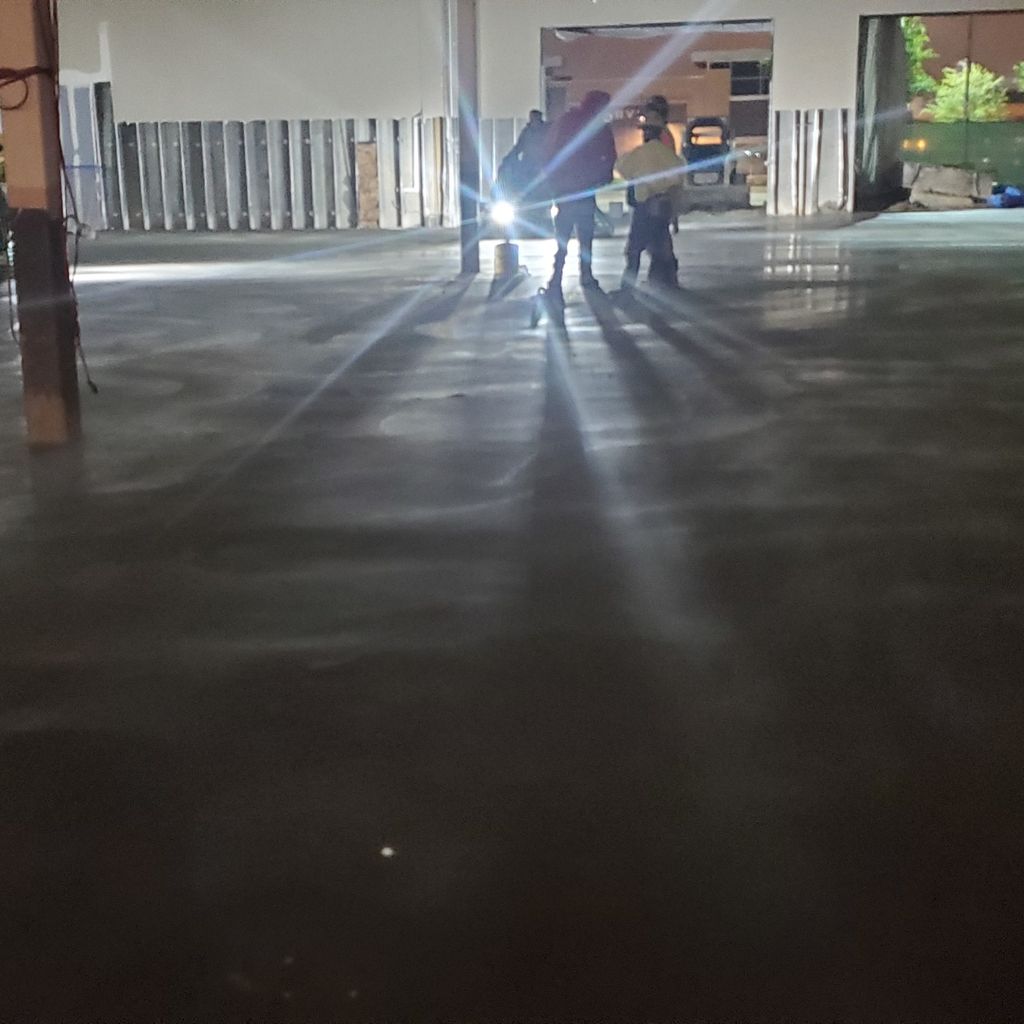
Commercial Concrete Services
IMPROVE YOUR PROPERTY WITH CONCRETE CONSTRUCTION WORK
Make your property more welcoming by adding ADA-compliant sidewalks and parking lots. Boone Construction Services can install these and any other type of commercial concrete work in the Weatherford, TX and surrounding Dallas-Fort Worth areas, including Arlington, Mansfield, Aledo, and Irving, TX.
Our commercial concrete construction work also includes building:
- Paved lots and walkways
- New foundations
- Other types of concrete replacement
Call 817-901-6650 now to speak with a concrete contractor about your commercial concrete project.
Concrete Demolition
Between the ever-changing Texas weather, that good ol’ black gumbo dirt we have around the Dallas Fort Worth Area, the expansion and contraction can crack concrete and leave it in need of being repaired, replaced, and demoed. Industrial Concrete Solutions specializes in concrete breakout and replacement for all types of concrete: concrete parking lots, concrete driveways, and industrial or commercial floors, or any concrete flatwork. To minimize the discomfort, we strive for the fastest turnaround time as possible. Speed, quick turnaround, and communication are at our core beliefs for ICS. If you need a concrete contractor who specializes in concrete demolition with the know-how, please let ICS know. The cost of concrete demolition is driven by labor, haul-off, concrete sawing, equipment, and or rental.
Parking Lot Repair
Concrete Driveway Replacement
Concrete Parking Lot Replacement
Industrial Floor Replacement
Concrete patchwork
Concrete Parking Lot
Boone Construction Services has installed/placed many concrete parking lots throughout the years. We ensure our grades are accurate, the rebar is placed on high chairs, and the sub-base is treated to spec or industry standards. Rebar used in parking lots is typically smaller in diameter in north Texas (#3 or at most #4). Large rebar size doesn’t always equate to a stronger parking lot. If too large of rebar is used it can actually cause the parking lot to break up. Weld Wire Mesh in a parking lot is not recommended because it is usually not a thick enough gauge to do any good, too rusty, or not picked up in the pour correctly. We have broken out concrete too many times with the wire mesh located on the bottom of the concrete parking lots. Yes, welded wire mesh (WWR) (WWM) is slightly cheaper on average to install around Dallas or Fort Worth areas, but you stand a greater chance of having to replace the concrete. BCS believes it is better to spend a little more and use the rebar. Rebar is usually around 12% to 20% of the cost for a concrete parking lot. Sub-base and treatments vary depending on soil conditions, geotechnical reports/agencies and engineer preferences for parking lots in the Dallas and Fort Worth areas. Actual rebar or reinforcement material cost varies from 15% to 25% on the total parking lot job costs. Depending on the size of parking lot, a concrete pump can be used to ensure that the rebar or reinforcing will not be disturbed by the traffic of the concrete trucks, or too deep or too shallow ruts are formed. Typically a 3500 psi mixture is used on most parking lots around the DFW area. Concrete placed through a concrete pump is usually more consistent in strength throughout than poured from a truck. The concrete placement phase of the project for concrete parking lots is usually preformed best when striking from rigid screeds (i.e. pipe screeds, expansion screeds, etc.). Many times if wet screeds (floating in the desired thickness and striking to it) are used by themselves, concrete thickness has a greater chance of varying. Another good recommended method is using a laser screed to complete the leveling or screeding of the concrete surface of a concrete parking lot. Trawling machines are typically used to ensure a finish free of surface voids, holes and rough spots in the parking lot. Material cost for the concrete is typically 30% to 50% of the total cost for the parking lot depending on size. Control joints are cut in the concrete mechanically no more than 24 hours upon the finish of the concrete. Since all concrete cracks, control-joints allow the concrete to crack at prescribed locations. As concrete in the parking lot hardens it usually shrinks (also known as shrinkage). This is what typically cracks the concrete in the beginning. This is why it is important to input mechanical cut control joints within 24 hours. Also, concrete in parking lots will expand and contract based upon external elements such as rapid change in the weather or temperature. It is recommended that expansion joints be placed per the industry standards in the parking lot to give the concrete the ability to expand and contract without breaking the concrete as well. To ensure that water does not drip down and cause erosion in the sub-base through the expansion joints, a self-leveling joint filler is recommended to be used. A concrete curing compound can be sprayed onto the surface of the concrete parking lot to help ensure the water content stays within the concrete and can increase the hardening process. It is recommended that the parking lot is stripped 30 days from the time it is poured with a solvent-based paint due to the concrete off gasing. Water-based paint can be used to strip with for an interim parking lot painting solution. Fire lanes usually are usually coded for 6 to 7 inches in thinknes concrete and 24 feet width. All parking spots usually are 8 feet for compact cars and 9 to 10 for all other parking. All handicap parking spots cannot have a cross slope greater than 2% to meet ADA Handicap parking standards. The cost for a typical new concrete parking lot can vary between 3.5 to 8 dollars a square foot (this price does not factor in the cost of concrete demolition). The biggest factor in the per square foot cost of a parking lot is the number of square feet in the project. The greater the square in the concrete parking lot the lower the per square foot costs in the parking lot will be.
Lime Base Stabilization
Rebar
Accurate grades
Concrete Drive Way
Boone Construction Services as a concrete contractor we have poured many new concrete driveways within the Dallas Fort Worth Area. Concrete driveways in most residential neighborhoods are typically 12 feet wide or across. Typically most municipalities require that concrete approaches have to be inspected. Some require that any new concrete driveway, new concrete patio, new concrete curbs, new concrete foundations, or any new concrete flatwork be permitted and inspected on concrete work. The cost of permitting a concrete project is usually based on a percentage of the concrete total project costs. New concrete driveway typically costs between anywhere from 4 to 10 dollars a square foot in the Dallas and Fort Worth Area depending on size. Industrial and commercial/retail concrete Driveways are very common to the residential concrete permitting cost structure and requirements. About all new concrete approaches for a new commercial driveway or retail driveways will require the concrete to be at least 22nfeet across for the fire lanes. The most concrete thickness on new concrete roads, concrete streets, and concrete driveways will need to be a minimum of 6 inches. Concrete roads, concrete streets, and concrete driveways are typically poured thicker for most other concrete paving. The texture of concrete roads, concrete streets, or concrete driveways is usually grooved mechanically or broomed with a coarse hair broom across the direction of traffic. Economies of scale will drive down the square foot cost on concrete; the more square feet you have the lower the cost per foot should be for concrete roads and driveways.
Standard Finish
Exposed Aggregate
Stamped
Stained
Integral Coloring
Sealed
Concrete Foundation
As a concrete contractor in the Dallas and Fort Worth area, BCS has poured many different types of concrete foundations. A concrete foundation can be used to describe many different types of concrete work: concrete slab, concrete pad, and concrete flatwork. Usually, the design of your concrete foundation is based on the type of substrate or ground conditions the foundation will be resting on. A concrete foundation is typically started by first establishing your finish floor grade. Once the grade is established the forms for the concrete can be set in place. Typically all foundations will have a footing around the perimeter. The perimeter footings are usually at a minimum of 22” (inches) from top of concrete and 12” (inches) wide. There are also cross footings, running horizontally and vertically, which divide the concrete foundation evenly (waffle slab). The rebar used in footings will typically be #5 (5/8 inch) or #6 (3/4 inch). Stirrups are used to hold the rebar in place at their desired centers in the concrete foundation footing. At the corners or intersections of beams, rebar bent into 90 degrees will be used to connect the intersection of the rebar steel giving tied up continuously. The length of the 90s will change based on the size of the rebar being used. The larger the rebar the longer the overlaps will be required. Mostly cushion sand, select fill or lime stabilized dirt is used for grading the top surface of the make-ready. A vapor barrier or poly is used to keep water from coming up through the foundation and causing problems on the surface of the concrete. The recommended minimum depth of the concrete in a foundation is 4 to 6 inches or based upon the geotechincal report or engineering. For industrial or commercial or retail settings, concrete foundations are structural in nature or will have some weight placed on top; therefore Industrial Concrete Solutions recommends using 3500 psi concrete. To increase the strength of concrete a higher amount of Portland cement is used and this is nominal in the total cost of the concrete foundation project and also a high-level water reducer. The type of reinforcing used in the concrete foundation is mostly based on the substrate. The more clay the dirt contains the more the surface of the ground can be moved around. Many builders will combat this by installing a post-tension foundation. Post tension cables require re-tensioning every ten years due to the elasticity and elongation. ICS recommends rebar reinforcing. If the substrate contains a lot of clay, piers or larger footings can be added to support the foundation from being damaged from too much expansion of contraction. Piers or deeper footings can also be added if the concrete foundation will be used for heavy industrial or manufacturing uses. The cost of a concrete foundation can vary based on its intended use and square footage.
Concrete Construction
Concrete construction is building something from concrete. Since concrete is something that is costly, has a short life to work with it, and is a long-lasting fixture it should be performed by a skilled concrete contractor or a concrete professional to meet industry standards. The largest qualifier for a good concrete company is their construction experience, project management capabilities, and ability to stand behind their product. Industrial Concrete Solutions has mastered many concrete construction projects within the Dallas and Fort Worth area. Please let us assist you with your next project.
Concrete Design and Engineering
Not all concrete requires design and engineering to be performed by an engineer or architect. Many times Industrial Concrete Solutions has been asked to contribute to concrete design based on our pool of experience and understanding of the concrete industry. Recommendations and valued engineering suggestions were given by BCS have helped both engineers and customers stay within budget and perform the job faster than otherwise bid to do. BCS can be a value in assisting on a project not only in the construction phase but also in the design and engineering phase.
Weight and scale
A weight and scale system is a sophisticated, under-the-floor weighing system that is used primarily for weighing extremely heavy things, such as bulk shipments. Industrial Concrete Systems has installed such systems in past projects.
Heavey Equipment Pads
In your industrial or commercial environment, you will probably have a need for a foundation that is poured for greater than normal weight. Industrial Concrete Solutions has poured many of these slabs over the years in the Dallas and Fort Worth area. When your production is on the line you need a concrete contractor with speed and excellence to get in and safely complete your industrial slab. The square foot costs for these types of slabs vary in costs because they are uniquely designed around your machine base or equipment footprint.
Heavy Equipment Slabs
ADA Concrete Parking
BCS has performed the concrete breakout and replacement or new installation on handicap accessible parking meeting ADA compliance. As the market demands grow for safer and more compliant access into facilities, ICS has the solution and experience to assist you.
Concrete painting
Cross slope of 2% maximum
2% direction of travel
Concrete ADA Ramps
Industrial Concrete Solutions has performed concrete breakout and replacement of ADA ramps. As the market demands grow for safer and more compliant access into facilities, ICS has the solution and experience to assist you.
Concrete painting
Cross slope of 2% maxium
2% direction of travel
Ramp slope is 8.33% max slope
Concrete ADA Sidewalks
Boone Concrete Services has performed the concrete breakout and replacement or new installation on new side-walks to meet ADA compliance. As the market demands grow for safer and more compliant access into facilities, BCS has the solution and experience to assist you. Also for private concrete sidewalks or walking paths, BCS has installed many linear feet over the years.
ADA Compliant Sidewalks
Concrete Forklift Ramps
Need a ramp to your front door, back door, second-level, or anything else? Our access ramps are built under the highest standards of quality.
Equipment Ramps
Containment Pit Well
A containment pit of sump is a fluid collection reservoir set into the floor. It is useful for collecting chemicals that shouldn't be drained into normal sewage. A sump pump allows you to get this fluid out of the sump.
Conveyor Vault/Well/Pit
Concrete Containment Structures